- News Center
Company news
Industry information
- Stainless steel 06
- Stainless steel 07
- Stainless steel 05
- Stainless steel 03
- Stainless steel 04
- Stainless steel 01
- Stainless steel 02
- Aluminum castings 05
- Aluminum castings 04
- Aluminum castings 03
- Aluminum castings 02
- Aluminum castings 01
- Aluminum die-casting product 08
- Aluminum die-casting product 07
- Aluminum die-casting product 06
- Aluminum die-casting product 05
Company news
Position:Home > News Center > Company news
- The role of dry mold in the process of aluminum sand turning
- Editor:Hangzhou Hongcheng Pml Precision Mechanism LtdDate:2016-06-07 10:51 Click:
sand casting process has been a long time ago. The old foundry craftsmen were mainly forced to live, with a family with a small stove, the wind box and other simple tools, pushing small cars around the streets, repairing damaged ploughs, ploughshares, and broken iron pot for farmers. Later, the craftsmen continued to expand their organization and technology, and the target of mobile production began to target the city. For urban residents and business customers, and sell some cast iron products
the traditional sand casting process, also known as sand casting, is poured molten metal into the casting cavity, cooled and solidified, and then obtained by repairing and grinding. Hangzhou Hongcheng Pml Precision Mechanism Ltd inherits the traditional process of aluminum casting and sand casting, and with the development of science and technology, continuous progress and improvement, aluminum castings are used in many industries.
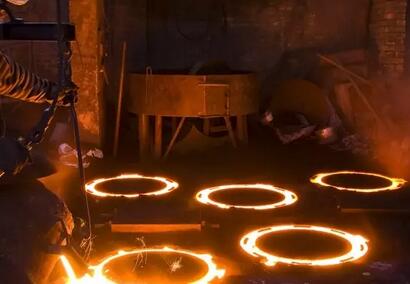
cast aluminum castings must first be made of cast iron moulds. The production of the dry mold is followed by the traditional Chinese traditional method. The clay is added into the proportionate sand and ash, and the water is stirred into the uniform mold mud, and then various shapes of mould are made according to the requirements of the product. With the mold, it can be turned into the cavity sand mold. When making sand mold, it is necessary to consider how to remove the mold from the upper and lower sand boxes, and to consider where the molten iron is flowing from, how to fill the cavity in order to get high quality aluminum castings. After the sand mold is made, it can be poured, that is, pouring molten iron into the cavity of the sand mold. When pouring, the temperature of molten iron is 1250&mdash, 1350 degrees, and the melting temperature is even higher.